In the intricate world of lithium battery assembly, achieving impeccable quality and stability is paramount. Among the myriads of critical processes involved, laser cleaning has emerged as an indispensable step, especially in sealing nail welding—a pivotal factor in determining the overall quality and dependability of lithium batteries. As the name suggests, cleaning is all about purging impurities or contaminants, and laser cleaning has become the method of choice. But how exactly does laser cleaning work its magic, and why does it leave no harm in its wake?
I. Unravelling the Laser Cleaning Process
The Power of Laser Cleaning:
In traditional cleaning methods, solvents and ultrasonic techniques have been commonly employed. However, these methods have their limitations. Solvent cleaning, for instance, struggles to eliminate residual electrolytes during battery injection, while ultrasonic cleaning can inadvertently damage the battery. This is where laser cleaning steps in as a game-changer.
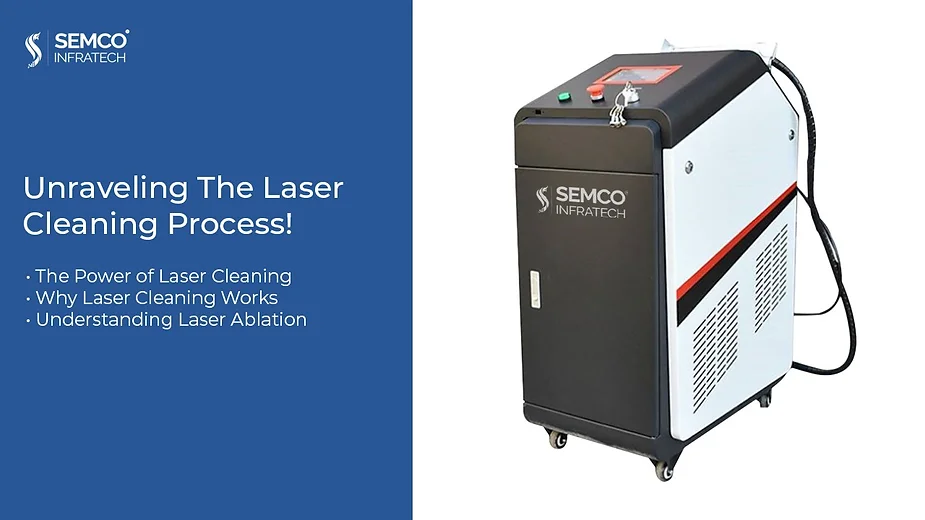
Why Laser Cleaning Works?
Laser cleaning harnesses the power of precisely tuned lasers. When a laser is focused, it can induce either laser ablation or photoablation on the surface of the target material. These processes involve the removal of material from solid or liquid surfaces by irradiation with a laser beam. At lower laser flux, absorbed energy heats and vaporizes or sublimates the material, while at higher flux levels, the material is often converted into plasma.
- Understanding Laser Ablation: Laser ablation typically pertains to the removal of materials using pulsed lasers. However, in cases where laser strength is exceptionally high, continuous-wave laser beams can also be employed for ablation. The depth of energy absorption and the quantity of material removed by a single laser pulse depend on factors such as material optical properties, laser wavelength, and pulse duration.
- Ablation Rate and Process: The total mass of material removed by each laser pulse is termed the ablation rate. Laser radiation characteristics, including scanning speed and line coverage, significantly influence the ablation process.
II. Application of Laser Cleaning in Lithium Battery Assembly
- Enhancing Welding Quality: In the realm of lithium battery assembly, especially during the cleaning of liquid injection ports, the substrates are often made of metals like aluminum. Pollutants to be removed typically include electrolytes, DMC, and other contaminants. Failure to clean these pollutants adequately can lead to issues like welding defects such as frying points and black spots. Proper cleaning ensures high production yields and weld quality.
- Parameters Impacting Cleaning: Various laser-related parameters influence the effectiveness of the cleaning process. These include laser energy density, wavelength, pulse width, number of pulses, and incident angle.
III. Key Parameters Influencing Laser Cleaning
- Laser Energy Density: This parameter is pivotal in laser cleaning. It must be within the range defined by the cleaning threshold (the minimum energy required to remove pollutants) and the damage threshold (the energy at which substrate damage occurs). Ideal energy density typically hovers around 80% of the damage threshold.
- Laser Wavelength: Different wavelengths have varying effects on materials. Shorter wavelengths result in higher material absorption rates, enhancing cleaning efficiency. The choice of wavelength depends on the nature of the pollutants and the substrate.
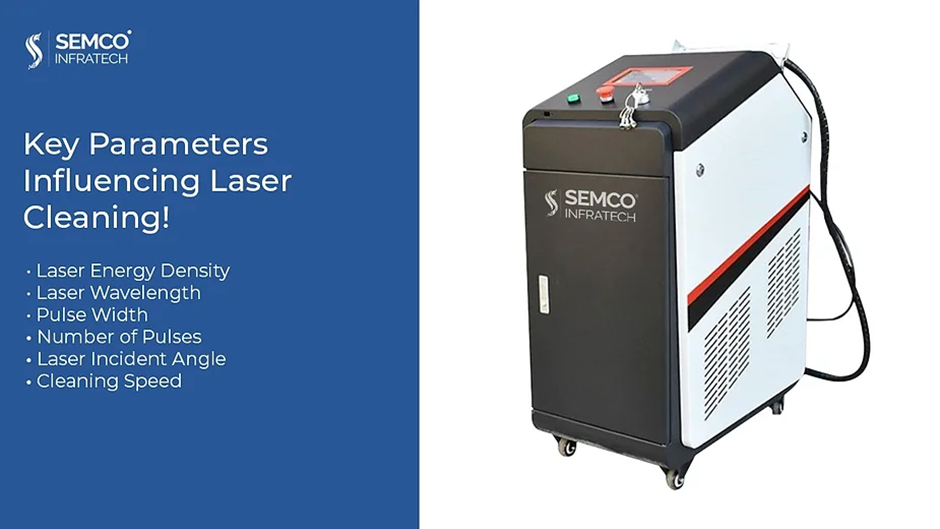
- Pulse Width: Also known as pulse duration, it affects thermal diffusion depth and material interaction time. Shorter pulse widths offer greater cleaning efficiency by focusing energy more effectively.
- Number of Pulses: While an increase in the number of pulses initially improves cleaning efficiency, there’s a saturation point where additional pulses yield diminishing returns.
- Laser Incident Angle: Manipulating the laser incident angle can enhance cleaning efficiency by ensuring laser beams reach particles not directly exposed.
- Cleaning Speed: The speed of cleaning directly impacts energy density, with lower speeds requiring higher energy densities for effective cleaning.
Conclusion:
Laser cleaning has revolutionized the assembly of lithium batteries by providing a precise, efficient, and damage-free method to remove contaminants. Understanding the crucial parameters involved in laser cleaning is essential to ensure effective and reliable results. With laser technology continually evolving, its application in lithium battery production promises to play a pivotal role in maintaining high-quality standards and advancing the capabilities of these essential power sources.