The performance of lithium-ion batteries (LIBs) is significantly influenced by the characteristics of their separator diaphragms. Among the various types, the dry and wet diaphragms play a crucial role in determining battery efficiency, lifespan, and safety. In this blog, we will explore the differences between dry-process and wet-process diaphragms, their impact on battery performance, and how industries select the ideal separator for high-energy-density applications.
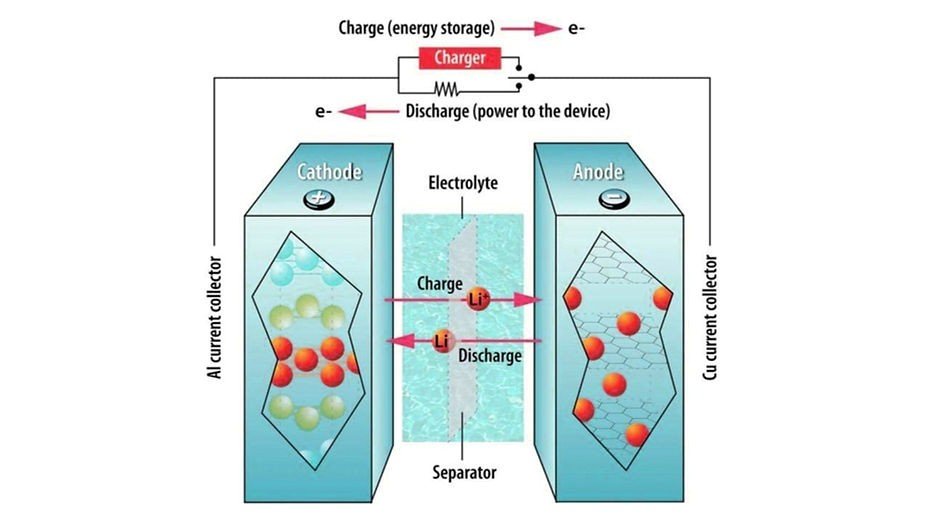
Understanding the Dry-Wet Diaphragm in Lithium-Ion Batteries
A diaphragm (separator) is a thin, porous membrane placed between the anode and cathode to prevent short circuits while allowing the passage of lithium ions. The two major types of diaphragms used in lithium-ion batteries are:
- Dry-Process Diaphragm: Manufactured using mechanical stretching, resulting in a more rigid and heat-resistant structure.
- Wet-Process Diaphragm: Made through solvent extraction, which creates a more uniform and highly porous structure, enhancing electrolyte retention and ionic conductivity.
How Dry and Wet Diaphragms Affect Lithium-Ion Battery Performance?
1. Electrochemical Performance and Conductivity
The wet-process diaphragm has a higher porosity, allowing more electrolyte absorption, which enhances ionic conductivity and battery efficiency. This leads to improved charge-discharge rates and better cycle stability. On the other hand, dry-process separators have lower porosity, reducing electrolyte uptake and slightly limiting ion transport.
2. Thermal Stability and Safety
A major concern in lithium-ion battery safety is thermal runaway, which can lead to battery fires and explosions. Dry-process diaphragms exhibit superior heat resistance, maintaining structural integrity even at high temperatures. This makes them ideal for applications where battery overheating is a risk. Meanwhile, wet-process diaphragms tend to shrink or degrade faster under excessive heat, potentially leading to short circuits.

3. Mechanical Strength and Durability
In terms of mechanical strength, dry-process diaphragms are more rigid and offer better puncture resistance, making them ideal for high-power applications like electric vehicles (EVs) and power tools. Wet-process diaphragms, due to their higher porosity, are more delicate but provide superior ion diffusion properties, benefiting energy-dense applications such as portable electronics.
4. Manufacturing Cost and Scalability
The cost of lithium-ion battery production is a critical factor in large-scale applications. Dry-process diaphragm production is cost-effective and has a simpler manufacturing process, reducing overall battery production costs. However, wet-process diaphragms, while expensive due to solvent extraction steps, offer better battery performance in high-end applications like EVs and energy storage systems.
Choosing the Right Diaphragm for Lithium-Ion Batteries
Manufacturers select the appropriate diaphragm based on the application, performance requirements, and cost considerations.
- Dry-process separators are preferred for high-safety applications (e.g., automotive batteries and industrial storage).
- Wet-process diaphragms are widely used in energy-dense applications (e.g., consumer electronics, laptops, and smartphones) due to their superior electrolyte retention.
Conclusion
The dry-wet diaphragm has a profound impact on the performance, longevity, and safety of lithium-ion batteries. While dry-process diaphragms offer better heat resistance and durability, wet-process diaphragms provide enhanced electrochemical performance and higher energy efficiency. The selection of the right separator is crucial for optimizing battery performance, making it a key factor in the advancement of next-generation lithium-ion batteries.
By understanding the role of dry and wet diaphragms, battery manufacturers can enhance the efficiency, safety, and longevity of their lithium-ion battery designs, ultimately shaping the future of energy storage solutions.