As the demand for energy storage systems continues to grow in industrial and commercial sectors, manufacturers are increasingly focusing on enhancing cost efficiency, production flexibility, and output quality.
A crucial driver behind this shift toward more sustainable and economically viable energy solutions is the integration of advanced battery-making equipment and universal machines into the lithium-ion battery assembly process.
These innovations transform how businesses approach energy storage production and deliver significant benefits across the manufacturing process.
The Need for Precision in Energy Storage Systems
Energy storage systems, particularly those used in large-scale applications, require highly precise and scalable manufacturing setups. In this context, energy storage devices such as lithium-ion batteries have become the backbone of modern electrical grids, consumer electronics, and electric vehicles. To meet the ever-increasing demand for these systems, manufacturers must ensure that their production processes are both efficient and adaptable. Modern battery-making machines serve as a critical part of this evolution, offering solutions that not only optimize cell production but also significantly reduce manual labour and minimize operational downtime.
One of the key advancements in this area is the development of the battery cell-making machine. These machines are designed to deliver consistent, high-quality cells that are crucial for module integration. The precision and repeatability they offer are non-negotiable, especially when it comes to meeting the stringent performance standards required for energy storage applications.
By automating and optimizing cell production, businesses can ensure that their products are manufactured to exact specifications, leading to higher reliability, longer lifespans, and improved overall efficiency.
The Role of All-in-One Machines in Battery Manufacturing
In addition to battery cell-making machines, companies are increasingly turning to All-in-One Machines and All-in-One Welding Machines—highly versatile systems that integrate multiple functions within a single unit. These multi-functional machines are designed to perform welding, assembling, and testing all in one streamlined operation.
The result is a dramatic reduction in production time, less manual intervention, and improved consistency across the manufacturing process. These machines also enhance quality control by providing real-time testing and adjustments throughout the production process, ensuring that each battery unit meets the necessary performance standards before it moves to the next stage.
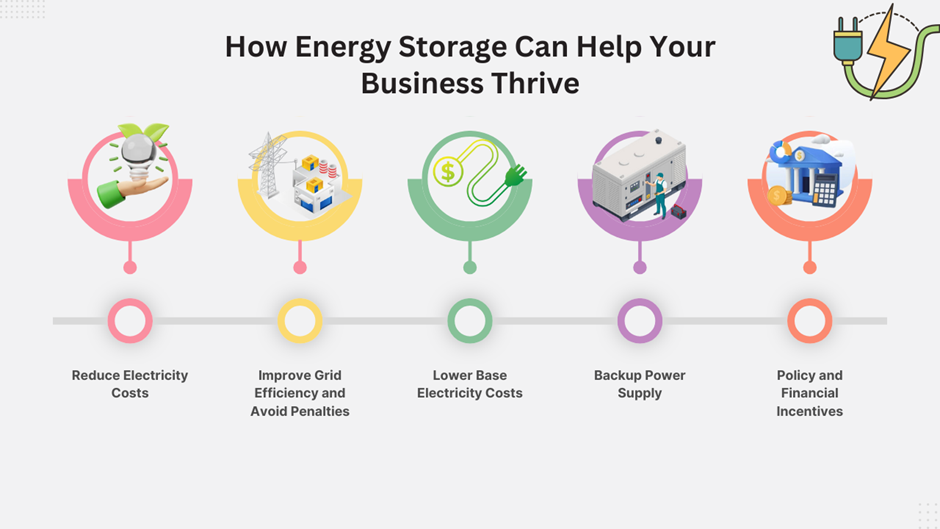
The benefits of using All-in-One machines are particularly evident in industries where time is of the essence, such as electric vehicle (EV) manufacturing and renewable energy storage. The reduction in production time not only lowers operational costs but also increases throughput, enabling manufacturers to meet rising demand without sacrificing quality. This makes them an invaluable asset for companies looking to scale up production while maintaining the highest standards of efficiency and performance.
Flexibility in Battery Pack Assembly
One of the major advantages of using universal battery-making machines is their ability to adapt to various types of battery cells. Whether it’s cylindrical, prismatic, or pouch cells, modern battery-making equipment can handle different form factors without requiring significant reconfiguration. This versatility is particularly important for manufacturers involved in lithium battery pack assembly, where multiple cell types may be used in different applications.
By investing in universal equipment that can seamlessly switch between different battery formats, companies can reduce space requirements and avoid the need for specialized machines dedicated to each type of cell. This results in lower overall equipment costs, better use of floor space, and enhanced flexibility in production.
The ability to switch between different cell types with minimal downtime also ensures that manufacturers can respond more quickly to changes in market demand, making their production lines more agile and capable of accommodating a wide range of products.
Boosting Return on Investment (ROI) and Grid Resilience
For businesses exploring the adoption of energy storage as a cost-saving measure, investing in high-quality, automated battery-making equipment and universal machines can significantly amplify their ROI. The integration of these machines not only increases production output but also helps manufacturers achieve better consistency in their products.
By improving the quality of their energy storage systems, companies can ensure that their products perform reliably over time, reducing the risk of failures and enhancing the overall reliability of the energy storage grid.
Additionally, by focusing on energy-efficient manufacturing processes, businesses can lower their operational costs, helping to offset some of the initial investment in new equipment. This results in a more sustainable production process, which contributes to long-term cost savings and a reduced environmental footprint.
Conclusion
As energy storage continues to play an increasingly critical role in modern industries, the need for high-efficiency, versatile manufacturing solutions has never been greater. For businesses seeking to reduce costs, increase production capacity, and improve product quality, investing in state-of-the-art battery-making machines and universal equipment is a smart choice.
These advanced solutions not only streamline the battery manufacturing process but also enhance the flexibility, scalability, and precision necessary to meet the growing demands of the energy storage sector.
By incorporating universal battery making machines into their production lines, businesses can achieve significant cost savings, boost throughput, and improve grid resilience—all while positioning themselves for long-term success in an increasingly competitive market.