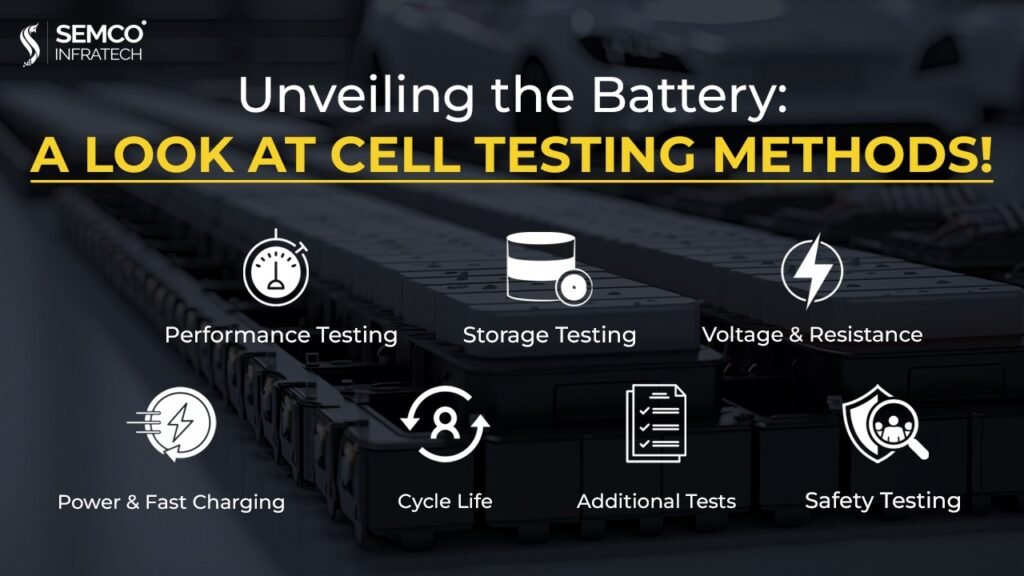
Ensuring the safety and performance of electric vehicle batteries requires rigorous testing of individual cells. This article explores various methods used to evaluate cell health and characteristics.
Performance Testing:
- Room Temperature Discharge: Cells are discharged at a specific rate (e.g., 1C) and then charged with a small current to remove polarization effects. This cycle is repeated to measure the cell’s capacity at room temperature.
- Rate Capability: Cells are discharged and charged at different rates (e.g., 0.33C, 1C, 2C) at a specific temperature. Higher rates may provide more capacity but also generate more heat.
- Efficiency: This test measures the energy lost during charge and discharge cycles. It helps assess the cell’s ability to utilize available energy.
Storage Testing:
- Capacity Retention: Fully charged cells are stored at different temperatures for varying durations. Their capacity after storage is compared to the initial capacity to assess their ability to retain charge over time.
- High Temperature & Humidity: Cells are stored in a hot and humid environment to test the reliability of their packaging.
Voltage and Resistance:
- SOC-OCV: Cells are charged and then left at different temperatures to reach a specific State of Charge (SOC). The open-circuit voltage (OCV) is measured at each SOC level, providing insights into cell behavior.
- Internal Resistance: This test measures the cell’s resistance to current flow at different temperatures and SOC levels. Higher resistance indicates a potential performance degradation.
Power and Fast Charging:
- Pulse Power: Cells are discharged or charged for a short period at high currents to assess their ability to deliver or accept bursts of power.
- Fast Charging: Cells are subjected to fast-charging protocols at different temperatures. Charging time and cell health are monitored over extended cycles.
Cycle Life:
- Cycle Testing: Cells are repeatedly charged and discharged to simulate real-world usage. This test evaluates capacity retention over a number of cycles.
Additional Tests:
- Specific Heat Capacity: This test measures the amount of heat required to raise the cell’s temperature by a specific degree.
- Disassembly: Cells are disassembled after charging or cycling to inspect the electrode interface for abnormalities.
Safety Testing:
- Thermal Runaway: Cells are subjected to conditions that may trigger thermal runaway, a dangerous overheating event.
- Overcharge/Discharge: Cells are deliberately overcharged or discharged to assess their safety margins.
- Physical Abuse: Cells are subjected to external short circuits, heating, impacts, and punctures to evaluate their ability to withstand abuse.
By employing these comprehensive testing methods, battery manufacturers ensure that individual cells meet the stringent performance and safety requirements for electric vehicles.
_____________________________________________________________________
About Semco – Established in 2006, Semco Infratech has secured itself as the number 1 lithium-ion battery assembling and testing solutions provider in the country. Settled in New Delhi, Semco provides turnkey solutions for lithium-ion battery assembling and precision testing with an emphasis on Research and Development to foster imaginative, future-proof products for end users.
For More Updates Follow Us
WhatsApp – Facebook – Instagram – Twitter – LinkedIn – YouTube