The lithium-ion battery assembly process is a meticulous journey that involves detailed planning, expert execution, and rigorous testing. Whether you are using advanced battery-making machines or semi-automated battery-making equipment, each step is vital to ensure performance, safety, and reliability.
Planning and Positioning: The Foundation of Success
Before starting the lithium battery pack assembly, it’s essential to focus on key layout and safety considerations.
- Protection Circuit Board Positioning: The protection board safeguards against overcharging, deep discharging, and short circuits. It must fit properly within the battery case.
- Battery Enclosure Compatibility: Ensure that the dimensions and layout of the board are compatible with the enclosure selected.
- Cell Configuration: Cylindrical cells are highly adaptable and work well in many battery cell-making machines. However, larger or soft-pack cells can impose space and layout limitations.
- Bracketing and Insulation: Use brackets to secure cells for increased mechanical stability. Where brackets aren’t feasible, robust insulation at contact points is crucial to prevent shorts.
Efficient Assembly Using Battery-Making Equipment
A well-executed lithium-ion battery assembly depends on optimal cell arrangement and structural integrity.
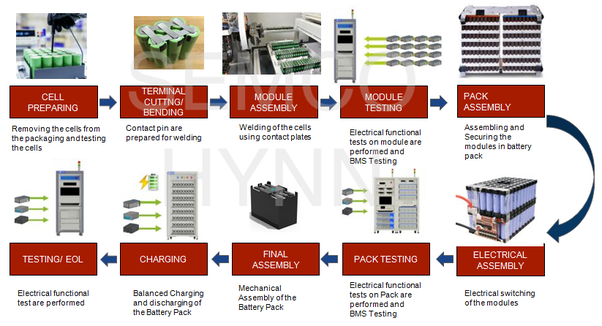
- Layout Matters: An inefficient layout can cause welding difficulties, packaging issues, and short circuit risks.
- Cell Fixation Methods:
- Without brackets, cells are secured with hot melt adhesive.
- Insulation strips are applied between cell rows.
- High-tensile tape reinforces the structure.
Welding and Interconnection
Precise welding is key in ensuring stable electrical connections, especially when using automated or semi-automated battery-making machines.
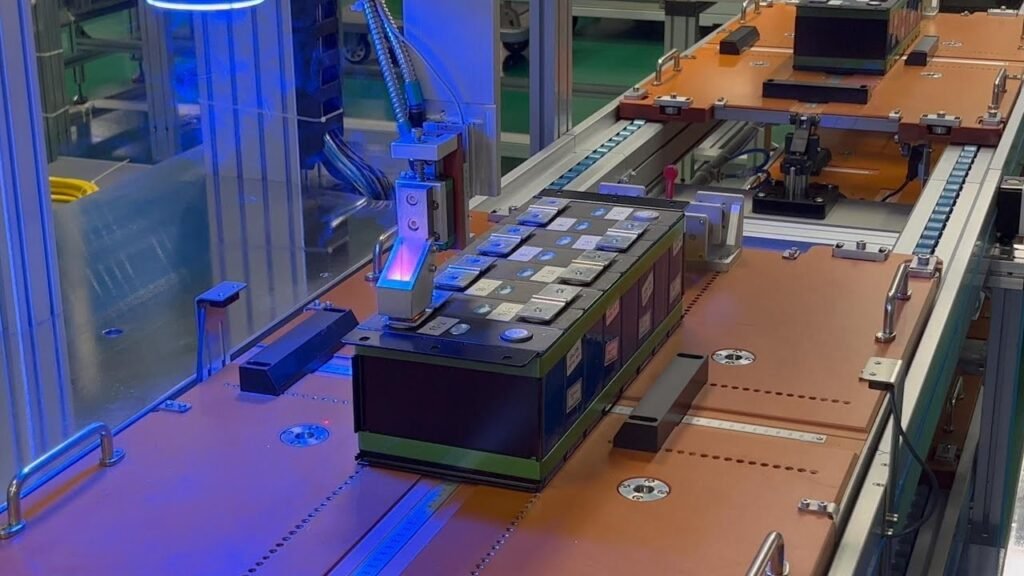
- Nickel Busbar Welding:
- Conduct test welds to fine-tune settings.
- Ensure clean surfaces and prevent overlapping.
- Align nickel sheets to avoid touching other cells.
- Wire Soldering on Protection Board:
- Perform clean and smooth soldering.
- Follow the proper welding sequence.
- Prevent slag from contaminating cell components or safety valves.
Rigorous Testing in the Battery Cell Making Process
Every lithium battery pack assembly must undergo a range of tests to validate functionality and safety:
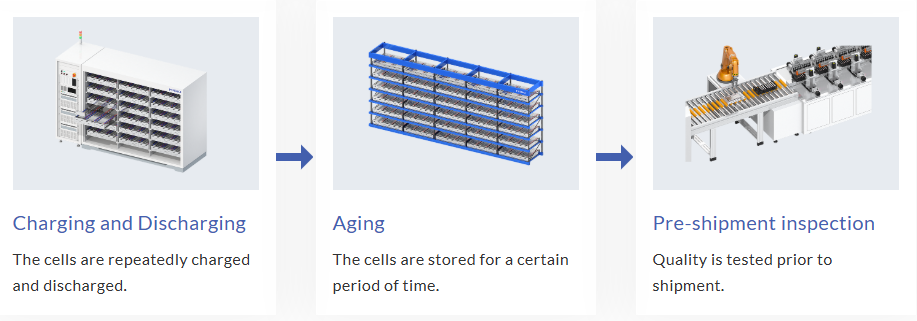
- Charging Test: Cells are charged under controlled current with temperature monitoring.
- Discharge Test: Identifies voltage imbalance between cell strings.
- Protection Board Assessment: Confirms proper cut-off and safety functionality.
Final Insulation, Shock Absorption, and Packaging
Protective steps finalize the lithium-ion battery assembly process:
- Wire Routing and Insulation: All conductors are insulated and routed safely.
- EVA Foam Installation: Shock-absorbing material cushions the cells.
- Heat Shrink Film: Provides waterproofing and enclosure.
- Encapsulation: Materials are chosen based on application needs.
Final Product Testing Before Deployment
To confirm performance, the finished pack undergoes:
- Open Circuit Voltage (OCV) Check
- AC Internal Resistance Testing
- Controlled Charging/Discharging
- Overcurrent and Short Circuit Testing
Conclusion:
By following this comprehensive process, powered by modern battery-making equipment and quality control protocols, manufacturers can ensure safe, reliable, and efficient lithium battery pack assembly—fit for electric vehicles, energy storage, and industrial applications.