The automotive industry is undergoing a rapid shift toward electrification, and at the centre of this revolution is the lithium-ion battery assembly process. As electric vehicles (EVs) dominate the future of mobility, automakers are making a bold move—investing in their own battery making machine and battery making equipment to take full control of battery production.
This strategic shift isn’t just about owning the technology—it’s about optimizing performance, reducing costs, innovating faster, and securing long-term success.
1. Reducing Costs & Gaining Production Control
EV batteries are among the most expensive components in electric vehicles. By investing in battery cell making machine systems and setting up in-house battery lines, manufacturers can reduce production costs significantly.
Having their battery-making equipment allows them to manage the full lithium-ion battery assembly process, from raw materials to final battery packs. This eliminates dependency on third-party suppliers, protects against market price fluctuations, and enables better scalability and customization.
For mass-market EVs, where cost-efficiency is critical, in-house lithium battery pack assembly can make a huge difference in profit margins and affordability for consumers.
2. Ensuring Stable and Reliable Battery Supply
Global demand for EV batteries is outpacing supply, and depending solely on a few external battery suppliers poses risks. Automakers who invest in their own battery-making machine and assembly units reduce their exposure to supply chain disruptions.
In-house production guarantees availability and supports ambitious production goals. With control over the battery cell making machine, they can ramp up manufacturing without delays caused by third-party bottlenecks.
This is particularly important as EV sales rise and governments around the world push for cleaner transportation alternatives.
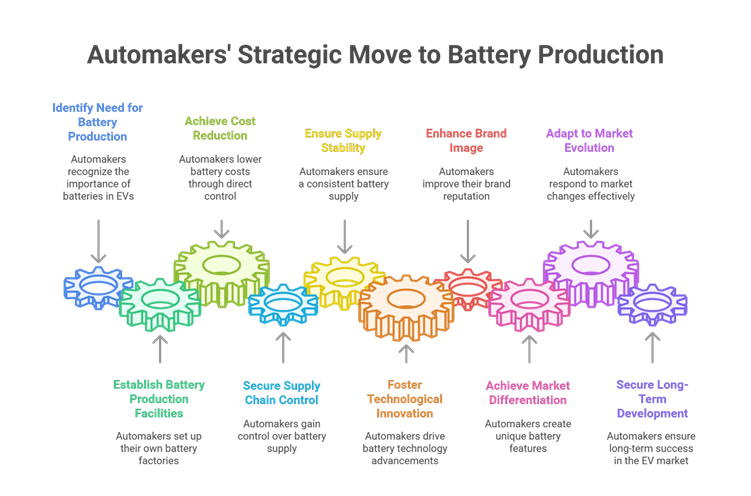
3. Boosting Innovation and Customization
By taking charge of the lithium-ion battery assembly process, automakers unlock new levels of innovation. They can test new battery chemistries, improve energy density, enhance safety features, and integrate proprietary battery management systems.
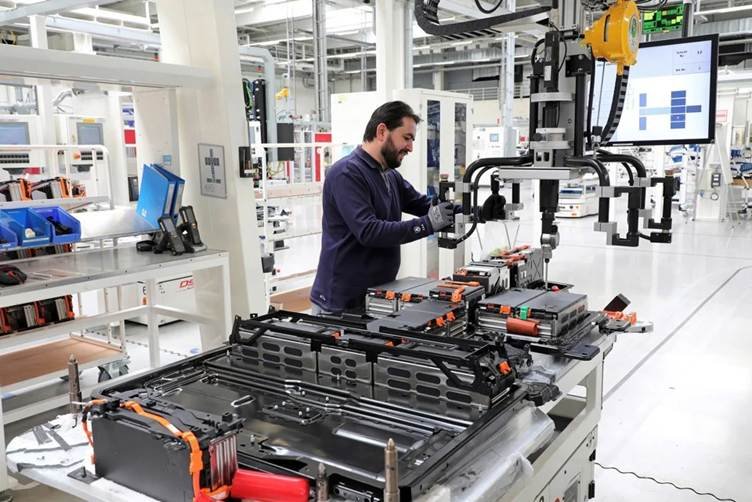
The data gathered during internal manufacturing helps improve the performance and longevity of batteries. Whether it’s faster charging or better heat management, these insights feed directly into R&D for next-generation EVs.
Having direct access to battery-making equipment also enables over-the-air (OTA) updates and fine-tuned battery optimization.
4. Enhancing Brand Identity and Market Positioning
Automakers with in-house lithium battery pack assembly capabilities are perceived as tech leaders. By producing custom-built batteries, they can differentiate their vehicles with advanced features such as longer range, quicker charging, and greater durability.
This positions their brand as a premium, future-ready choice for EV buyers. It also helps build trust—consumers are more confident in companies that own and control the critical components of their vehicles.
5. Preparing for the Future of Electric Mobility
Battery technology is evolving fast. Automakers with full control over the battery-making machine and lithium-ion battery assembly process are better equipped to adapt. They can quickly pivot in response to new regulations, raw material trends, or performance standards.
More importantly, in-house production aligns with a long-term vision of sustainable growth. It allows companies to reduce environmental impact, recycle components, and optimize production efficiency on a large scale.
Conclusion:
In-house battery production is no longer optional—it’s a strategic imperative. By adopting their own battery making machines, battery making equipment, and overseeing the battery cell making machine operations, vehicle manufacturers gain full control of the lithium-ion battery assembly process.
This empowers them to cut costs, ensure supply, lead innovation, and solidify their brand presence in the growing EV market.
As EV demand grows and battery technology advances, this move will be key to remaining competitive in the electric era of transportation.