Laser welding technology has revolutionized the manufacturing landscape, offering many advantages over traditional welding methods. This blog delves into the key characteristics of laser welding machines, exploring their impact on efficiency, quality, and versatility in various industrial applications, including lithium battery systems and lithium battery machine manufacturing.
Unmatched Efficiency
One of the most compelling attributes of laser welding is its exceptional efficiency. The highly focused laser beam boasts an intense power density, enabling rapid and precise welds. This translates to faster production cycles, particularly when dealing with large-scale automated welding tasks. Additionally, laser welding machines offer a wider repertoire of welding methods, including spot welding, splicing welding, and butt welding. This adaptability empowers manufacturers to address diverse welding needs within a single platform.
In industries such as lithium battery systems, where precision and reliability are paramount, laser welding machines ensure seamless and high-quality welds that enhance battery performance and longevity.
Hallmark of Quality
Laser welding produces high-quality welds that are both aesthetically pleasing and structurally sound. The narrow laser beam generates minimal heat input, resulting in welds with a small heat-affected zone and minimal distortion. This leads to smooth, high-quality weld finishes that meet stringent industry standards. The deep penetration capability of laser welding further enhances joint strength and weld integrity.
For lithium battery machine applications, maintaining high weld quality is crucial to ensuring battery reliability and optimal energy efficiency. Laser welding equipment is the preferred choice for welding battery cells, busbars, and other lithium-ion battery components with precision and durability.
Unveiling a World of Materials
The versatility of laser welding machines extends to a broad spectrum of materials. These machines excel at precision welding of various metals, including those known for their welding challenges. Beyond metals, laser welding can seamlessly join non-metallic materials like ceramics and organic glass. This adaptability makes laser welding machines ideal for diverse applications, from intricate electronic components to large, specially shaped workpieces.
In lithium battery systems, where different battery materials must be welded with high accuracy, laser welding technology ensures strong and defect-free joints, which are essential for battery pack longevity and safety.
Flexibility Redefined
Unlike traditional welding methods, which are often restricted by accessibility, laser welding machines offer unparalleled flexibility. The laser beam can precisely target and weld even in hard-to-reach or confined areas. This characteristic is invaluable for intricate components and complex geometries. Moreover, the precise positioning capabilities of laser welding machines ensure accurate and repeatable welds at the micron level.
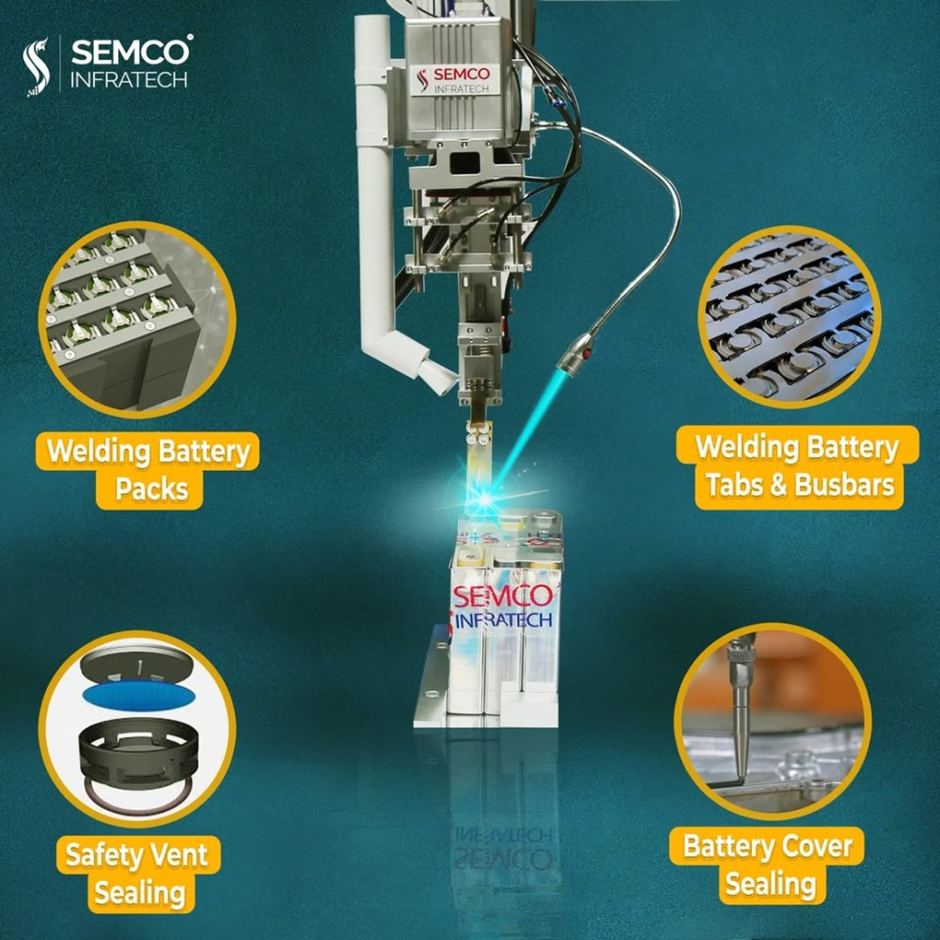
For lithium battery machine manufacturers, this flexibility enables the seamless welding of battery modules, cell casings, and busbar connections, reducing the risk of welding defects and ensuring long-term performance.
Durability and Reliability
Laser welding machines are renowned for their extended service life. With proper maintenance, these machines experience minimal downtime and require fewer repairs, leading to significant cost savings in the long run.
In lithium battery systems, where high-precision welding is crucial for ensuring battery safety and efficiency, laser welding equipment offers reliable and repeatable performance, making it an essential tool in battery production lines.
Speed, Depth, and Minimal Distortion
Laser welding boasts impressive welding speeds, enabling rapid completion of projects. The deep penetration capability ensures strong and reliable welds, while the minimal heat input reduces workpiece distortion. This eliminates the need for extensive post-weld corrections, making laser welding equipment particularly advantageous for applications requiring precise dimensional control.
For lithium battery machine production, fast and precise welding enhances battery assembly efficiency, reducing production time and ensuring high-quality connections for optimal battery performance.
The Future of Welding: High Precision with Laser Welding Machines
With their ability to achieve micron-level accuracy, laser welding machines are setting new standards in precision welding. Their exceptional quality, consistency, and efficiency make them the preferred choice for industries requiring the highest levels of precision and reliability.
As the demand for lithium battery systems and lithium battery machine manufacturing grows, laser welding technology will continue to play a critical role in ensuring efficient, durable, and high-performance battery solutions.