In the lithium-ion battery assembly process, precision is everything. One of the most critical stages is spot welding, which plays a fundamental role in the lithium battery pack assembly. This technique is used to securely join essential components such as nickel strips, battery cells, and protection plates, forming a durable and efficient battery pack.
The accuracy and quality of these welds significantly affect the battery’s performance, lifespan, and safety, making the right spot-welding machine and battery-making equipment vital to production success.
Why Spot-Welding Quality Matters?
Faulty welds in a battery pack can cause serious operational problems or even pose safety hazards. Here’s how different types of poor welds can impact performance:
- Weak welds: Can lead to poor connections that fail under vibration or pressure, often resulting in disconnection or energy loss.
- Incomplete welds: Result in gaps that may cause corrosion, current instability, or even short circuits.
- Overheating: If the welding process generates too much heat, it can damage the battery materials and reduce the overall battery efficiency.
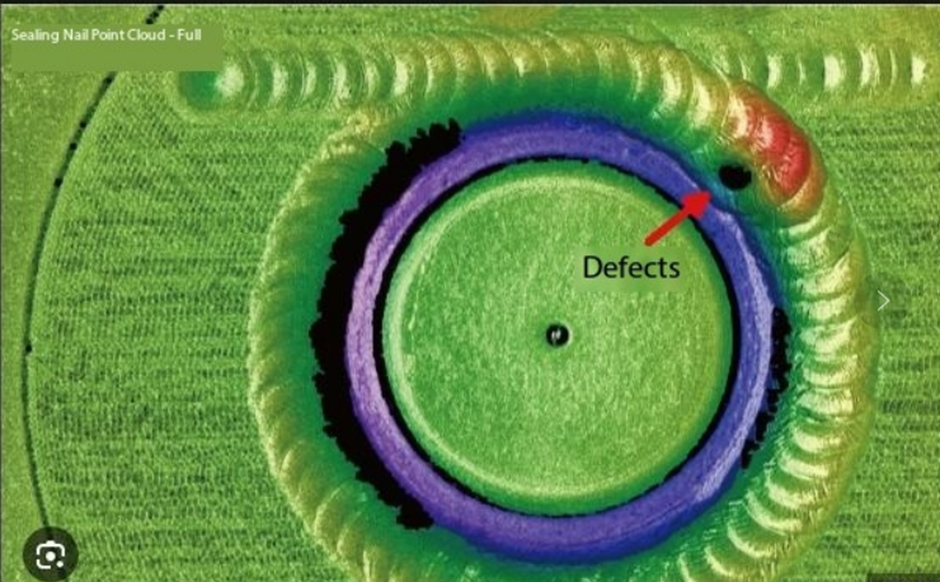
To avoid these risks, manufacturers must use advanced spot-welding machines for battery production and consistently monitor weld quality.
Understanding the Spot-Welding Process
In the battery cell making machine line, spot welding machines for lithium-ion batteries are engineered for speed, accuracy, and consistency. The battery welding process is generally divided into three key phases:
- Preparation: The cells are positioned and clamped in place. Here, welding parameters like power, pressure, and weld duration are adjusted according to the battery type.
- Welding: Using a lithium-ion battery spot welding machine, electrodes apply high current and pressure to fuse metal components, creating strong, reliable joints.
- Post-weld inspection: The welded battery pack is examined, cleaned, and tested to ensure it meets all performance and safety standards.
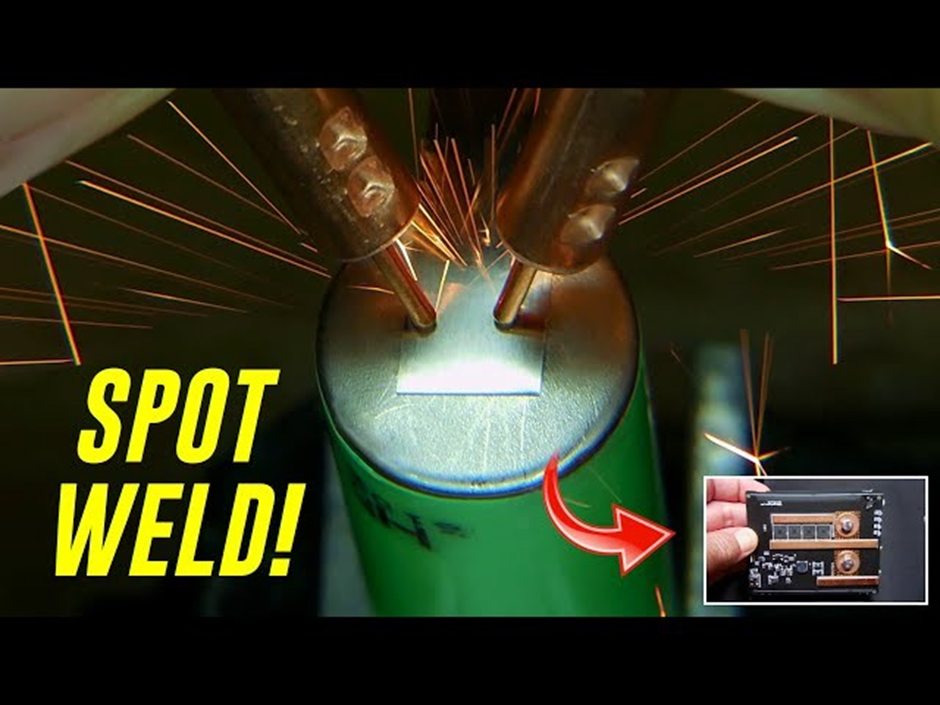
A reliable spot-welding machine for battery pack manufacturing minimizes errors, reduces waste, and enhances productivity in the battery-making machine line.
Environmental and Health Factors
Welding produces by-products like slag, metal dust, and electrode powder, which may pose both environmental and occupational hazards:
- Environmental concerns: If not managed properly, these by-products can enter water or air streams and cause contamination.
- Health risks: Workers exposed to fine particles may experience respiratory or skin issues if safety measures aren’t implemented.
Modern battery-making equipment includes built-in extraction systems and automated cleaning features to ensure both compliance and worker safety.
Selecting the Right Equipment
Using the right battery-making machine can make a significant difference in the efficiency and reliability of your production line. When choosing a spot-welding machine for lithium-ion batteries, consider:
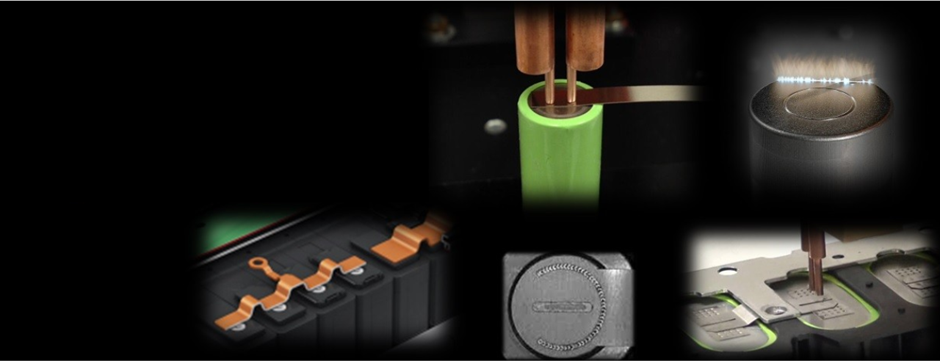
- Precision control: Machines should allow for accurate control over current, time, and pressure for consistent welds.
- Heat management: Excess heat can damage sensitive cells, so efficient heat control is a must.
- Low spatter operation: Less spatter means cleaner welds, fewer defects, and reduced post-weld processing.
Manufacturers who invest in high-quality battery cell making machines and battery making equipment are more likely to produce durable, safe, and high-performance lithium battery packs.
Conclusion
In the competitive world of energy storage, cutting corners on welding quality or using outdated equipment isn’t an option. By integrating top-tier spot welding machines, along with dependable battery making machines and battery making equipment, manufacturers can significantly improve both output and product reliability. The future of efficient, safe, and scalable lithium-ion battery assembly depends on both technical precision and the right tools.