


For Manufacturing Lithium-ion Batteries
Through Innovative Machines
For Manufacturing Lithium-ion Batteries
Through Excellent Service
For Manufacturing Lithium-ion Batteries
Through Research and Developement
Leading in Production Efficiency
Semco Infratech, a division of the Semco Group, distinguishes itself as a prominent player in lithium-ion battery production, testing, and assembly specializing in automation and digitization.
Semco Infratech operates in the market through key brands like Hynn & Neware. Established to cater to the growing demand for lithium-ion battery assembly equipment, Semco Infratech embodies a legacy of innovation and offers a wide range of products tailored to this sector for over two decades.

About Us
Our Services
Our Clientele
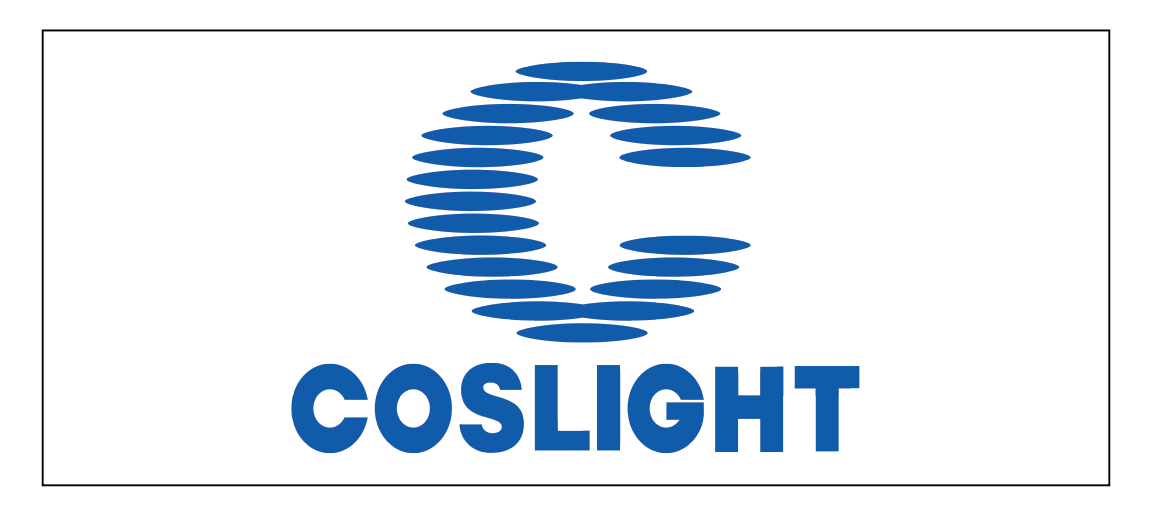
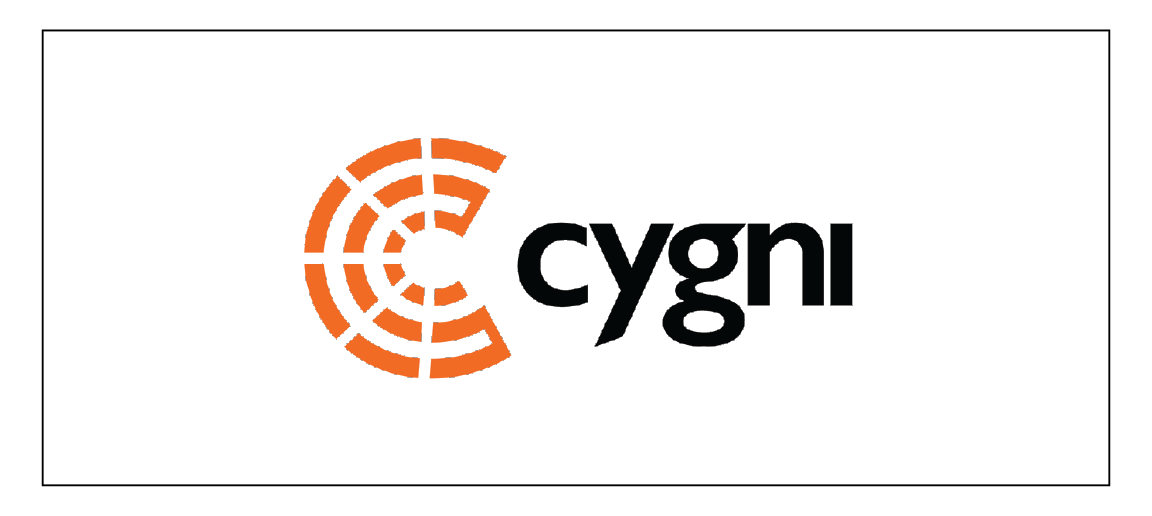
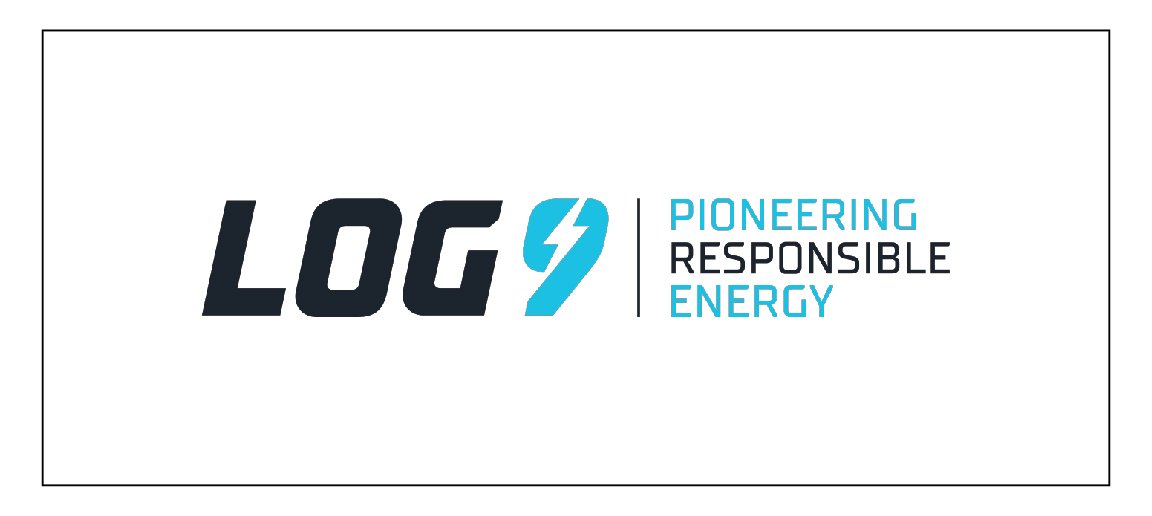


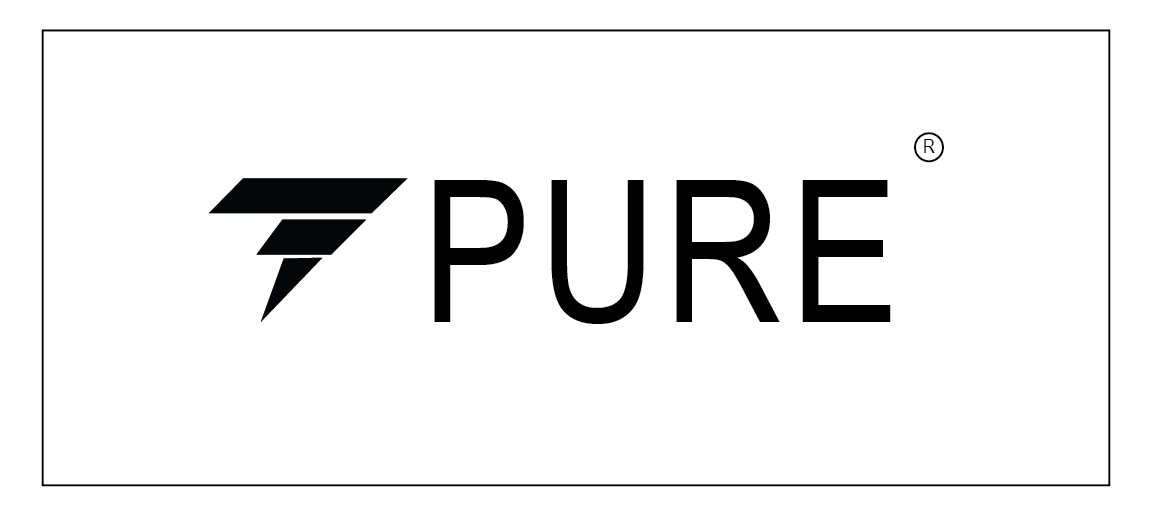

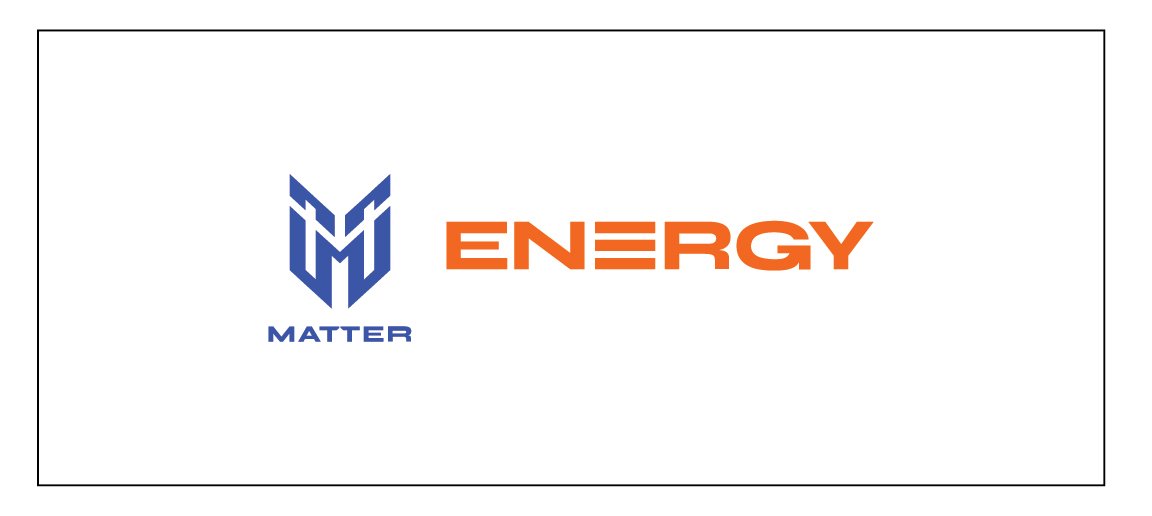




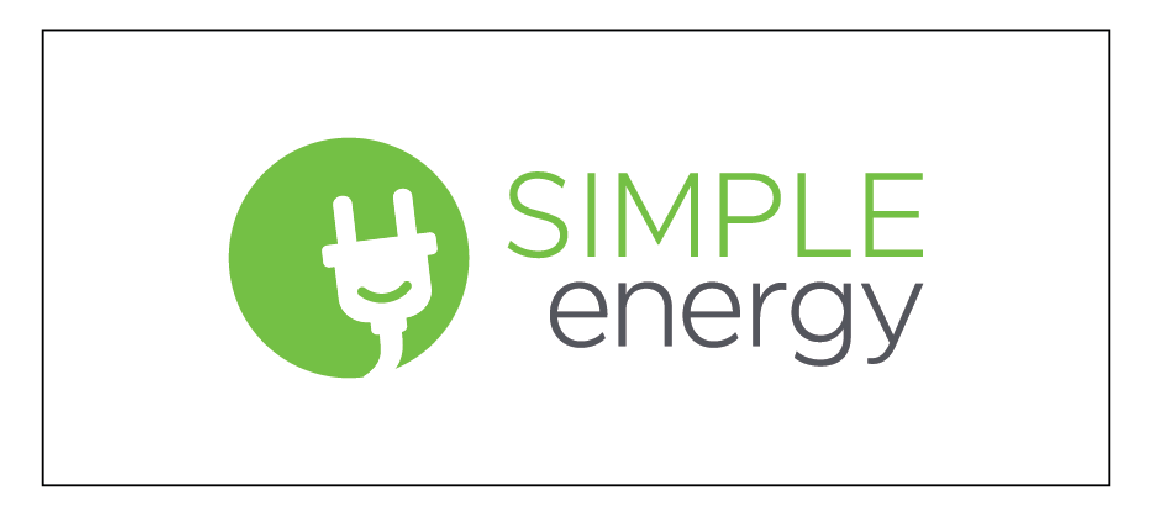
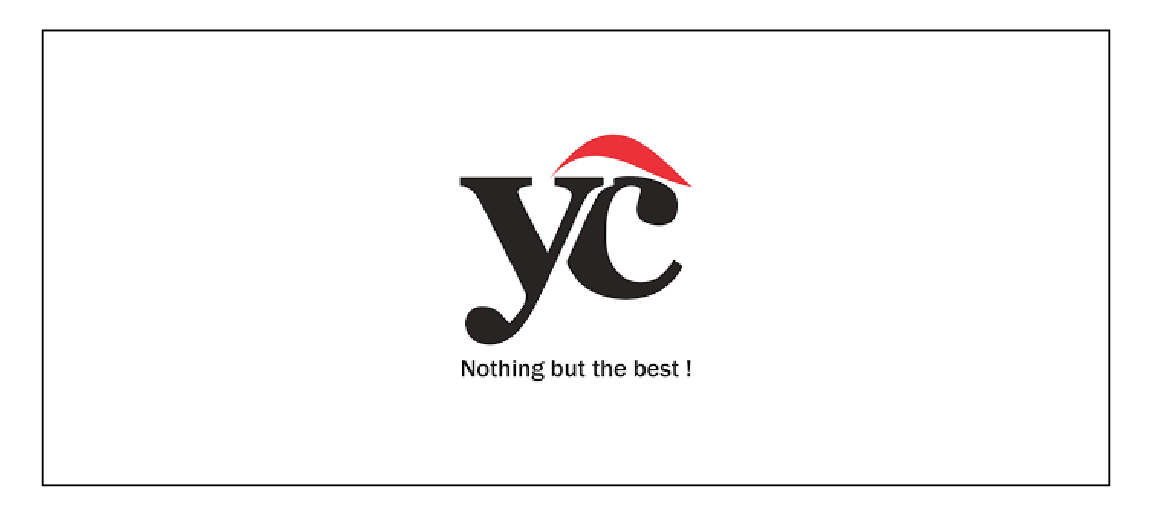
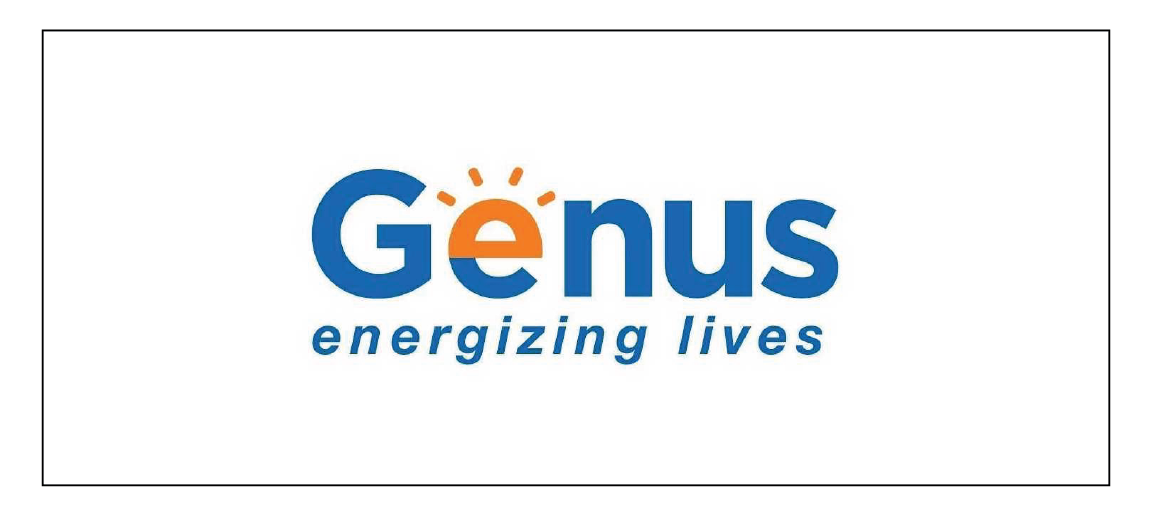
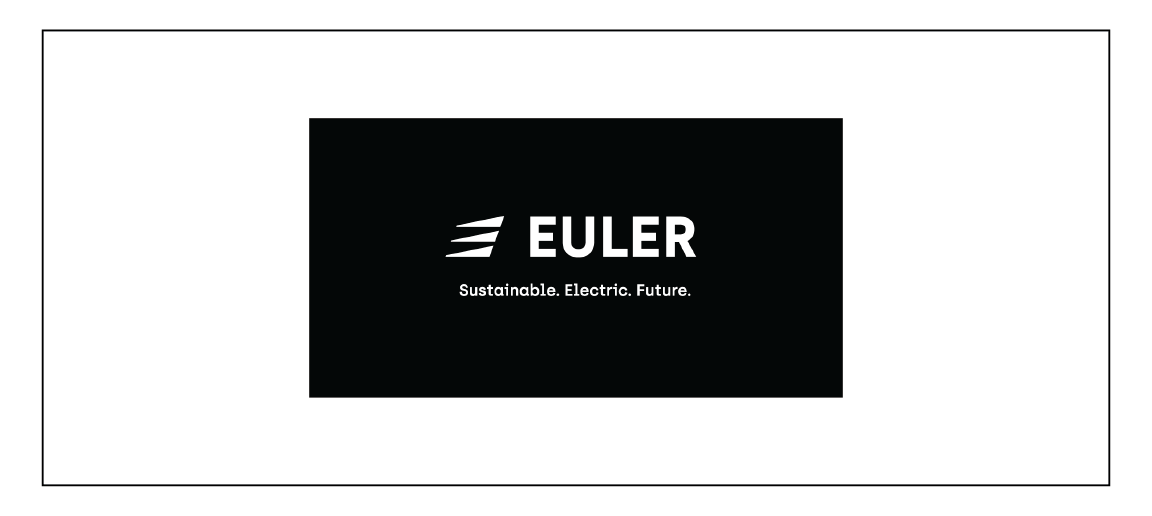
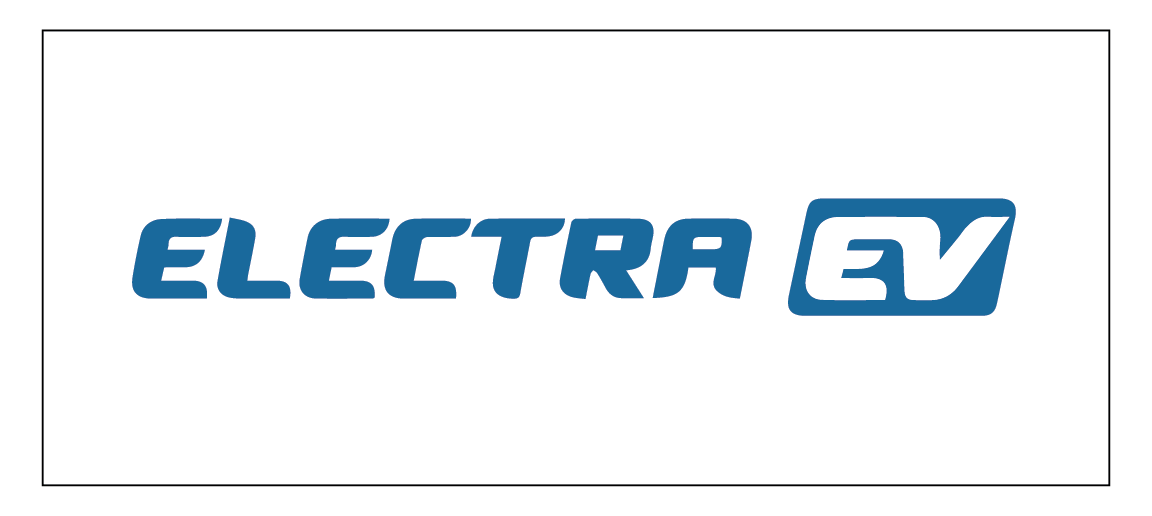

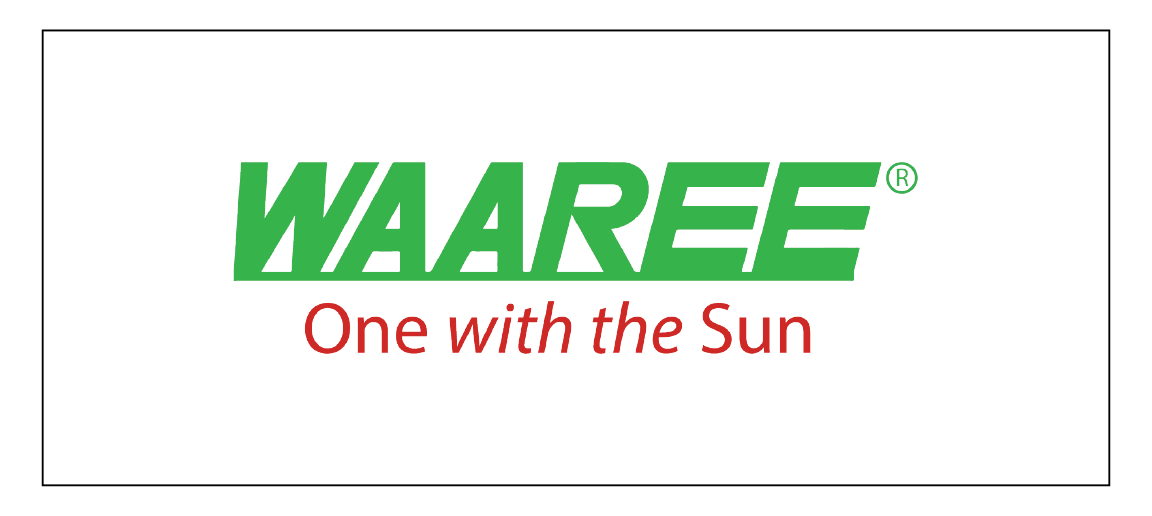
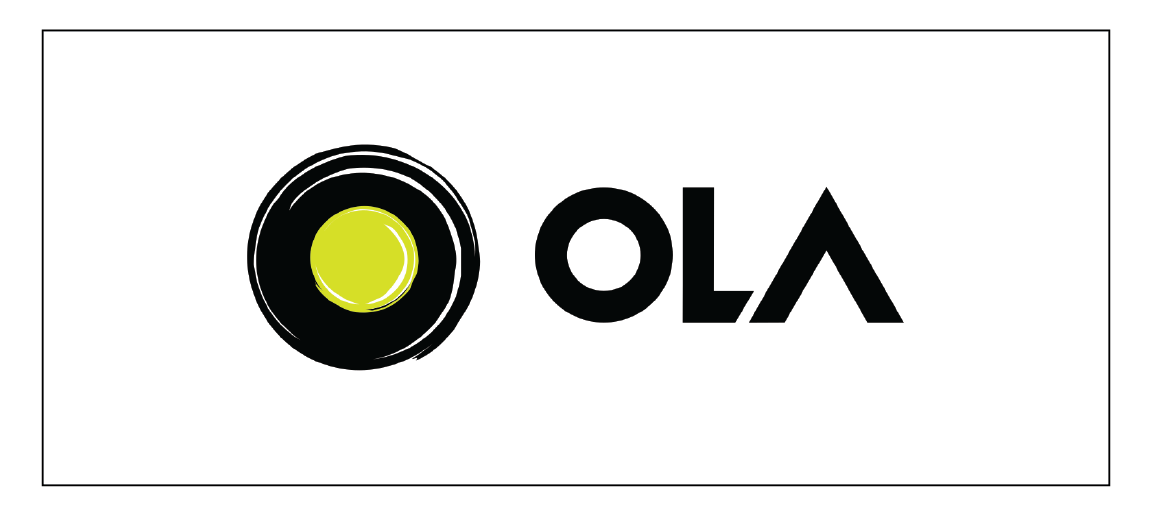

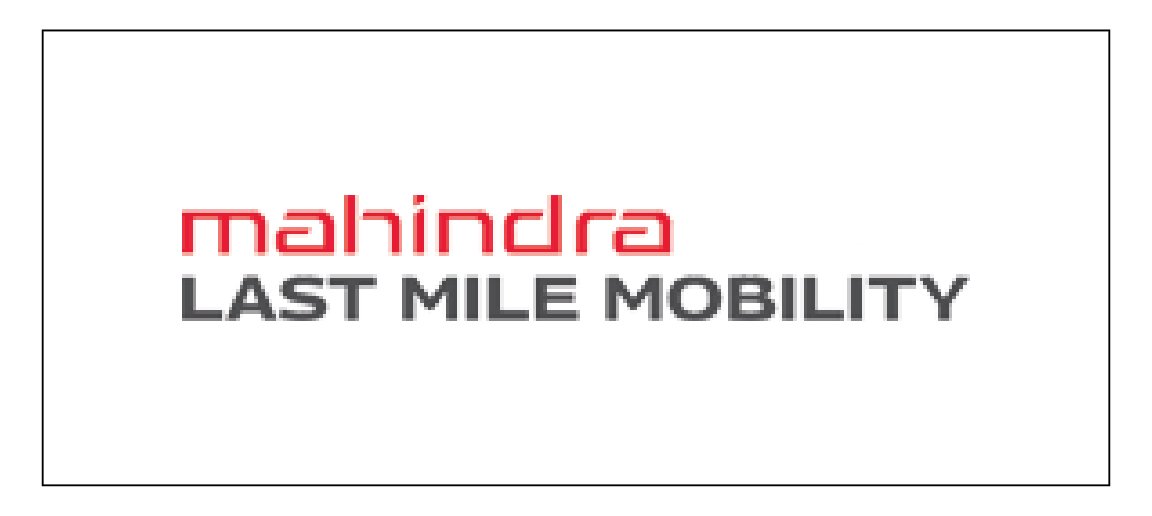
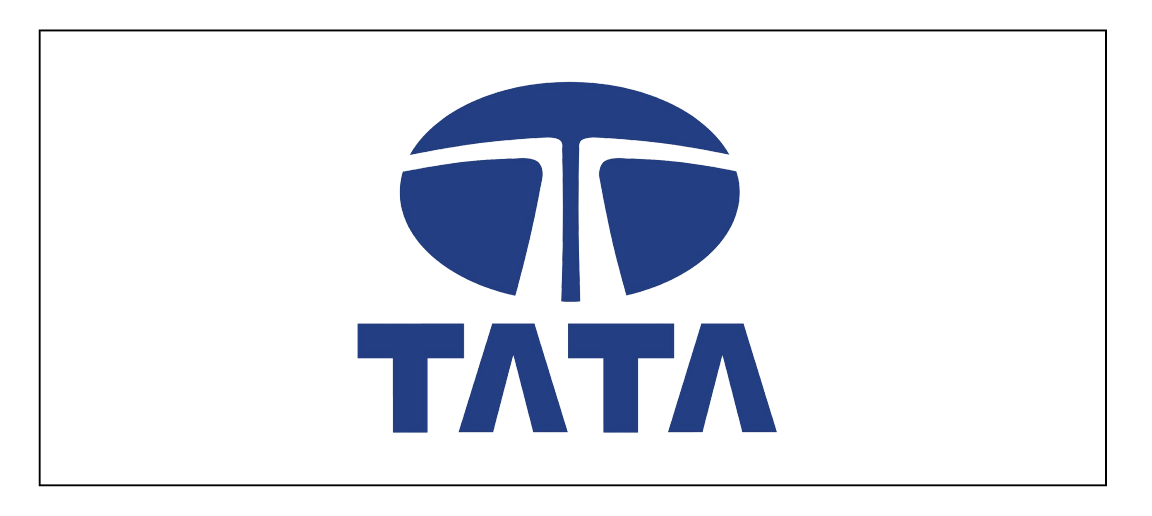
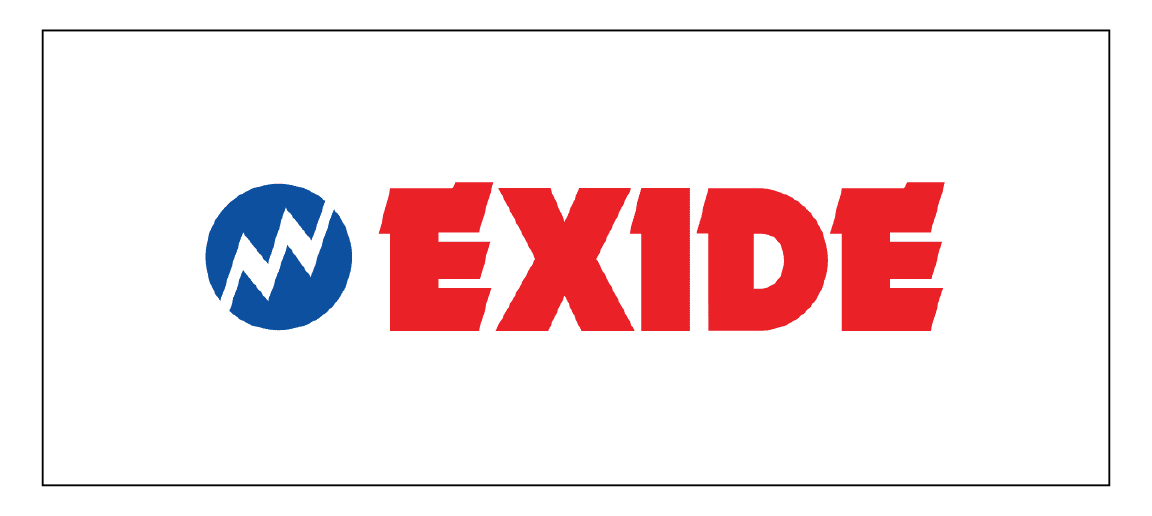

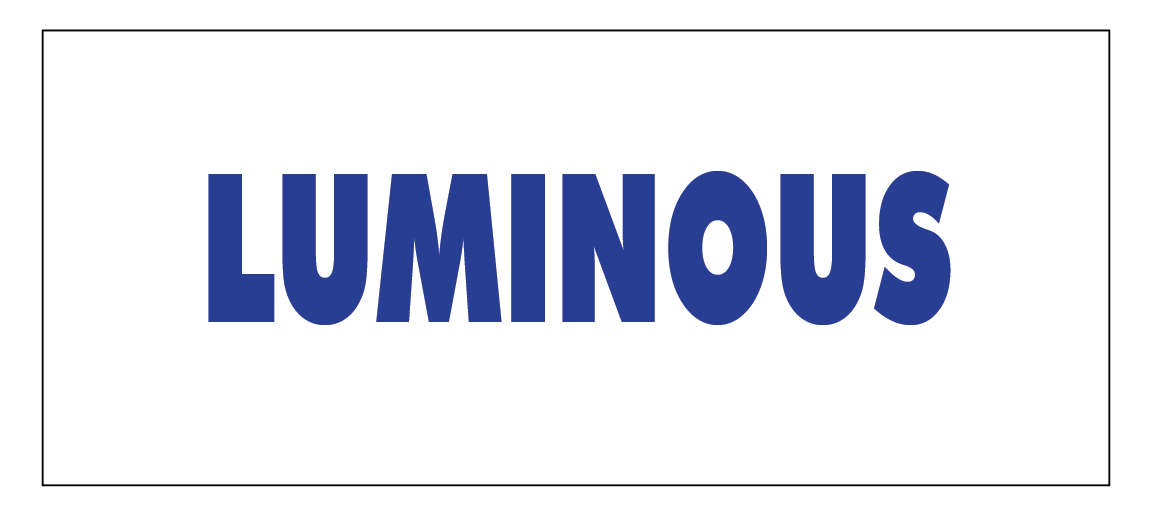
Testimonials
Azad Saini
Assistant Manager-Purchase
Luminous Power Technologies
Innovation and reliability are the hallmarks of Semco Infratech's exceptional service. Their lithium-ion battery testing machines and balancers have played a pivotal role in advancing our technological capabilities.
Manjeet Singh
Assistant Manager
Okaya Power Group
We have been working with Semco Infratech for several years, and they have consistently provided us with top-quality precision test and measurement equipment.
Devendra Chawla
MD & CEO
GreenCell Mobility
Semco Infratech's dedication to delivering high-value services and innovative technologies has greatly contributed to the success of our projects.
Rohit Kumar
Energy Storage Engineer
Thermax Limited
As a global leader in energy solutions, we rely on partners like Semco Infratech to provide us with cutting-edge equipment. They are fast, simple, and precise at their work.
Neha Sharma
Co-Founder, Gosporty
Semco Infratech has been an invaluable partner in our pursuit of excellence. Their commitment to delivering state-of-the-art precision test and measurement equipment has significantly enhanced our operational efficiency.
Mastering SOC: Accurate Diagnosis & Troubleshooting in Lithium-ion Batteries
Understanding the State of Charge (SOC) is crucial for maintaining...
Read MoreEmpowering Smart Manufacturing: The Rise of Fiber Laser Marking Machines
As industries rapidly shift toward customization, miniaturization, and automation, the...
Read MoreChallenges and Solutions in Welding and Forming Power Batteries
In the evolving world of lithium-ion battery manufacturing, the processes...
Read MoreOCV Tester Machine: Working, Mechanism & Importance
The Open Circuit Voltage (OCV) Tester Machine is a vital...
Read MoreBlogs
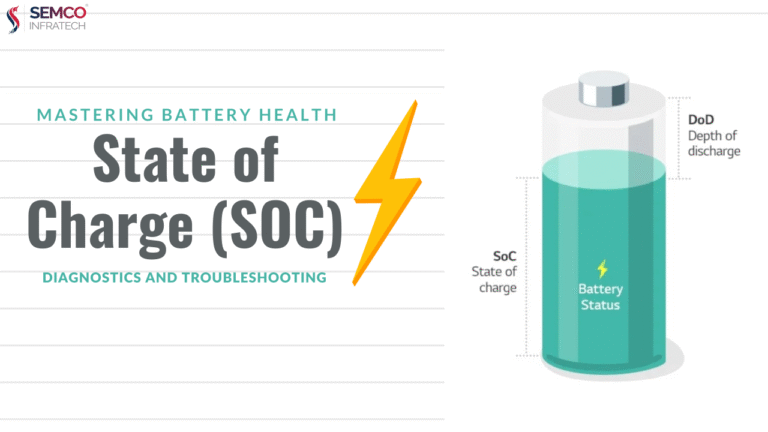
Mastering SOC: Accurate Diagnosis & Troubleshooting in Lithium-ion Batteries
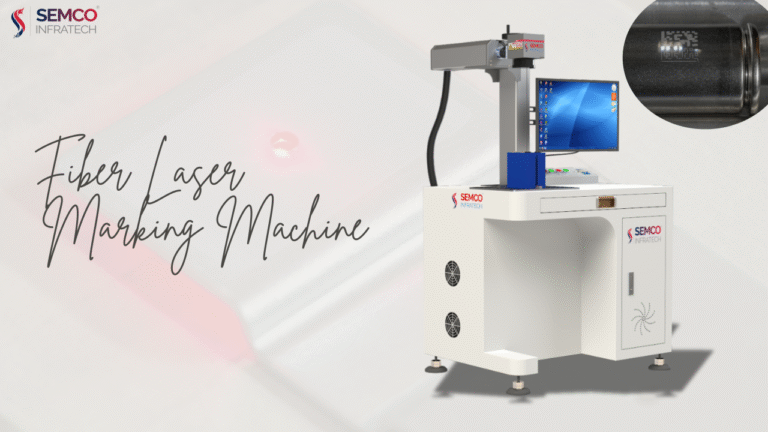
Empowering Smart Manufacturing: The Rise of Fiber Laser Marking Machines
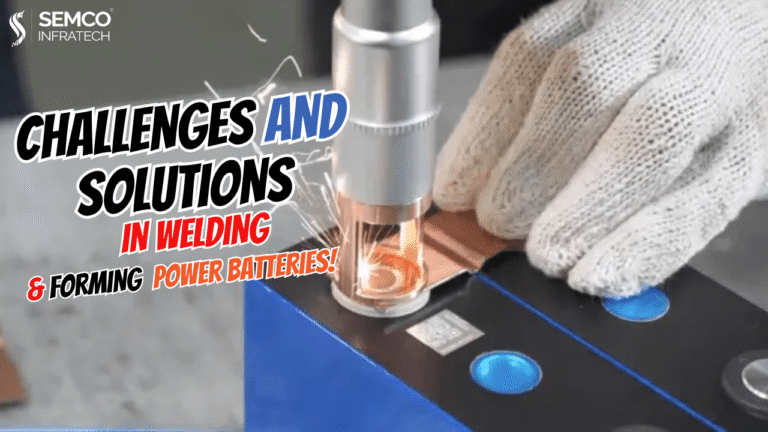
Challenges and Solutions in Welding and Forming Power Batteries
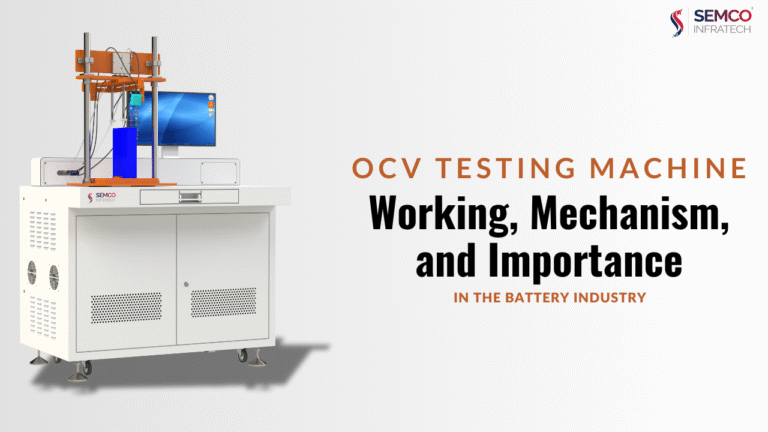
OCV Tester Machine: Working, Mechanism & Importance
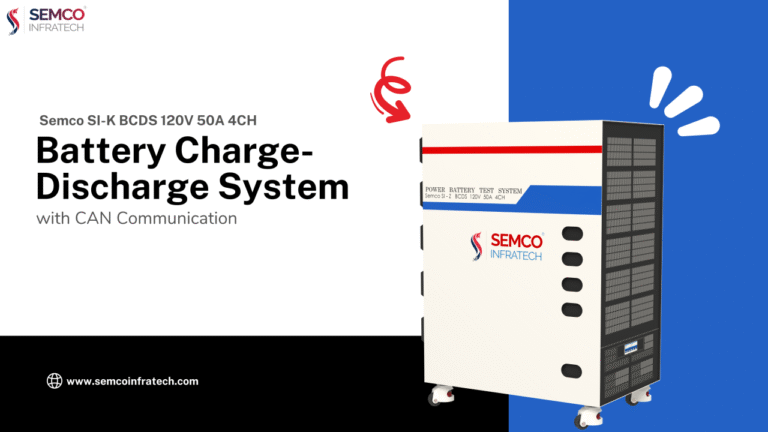
A Breakthrough in Battery Validation: Semco SI-K BCDS 120V 50A 4CH Explained
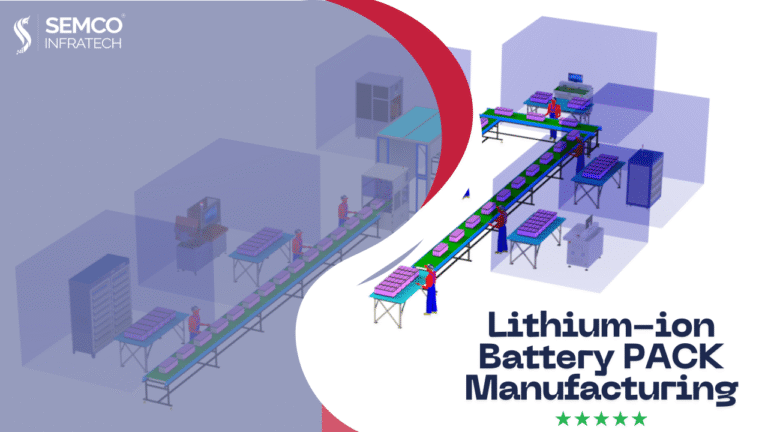
Lithium-ion Battery Pack Assembly: Techniques, Testing & Challenges
Events

The Smarter E India 2025
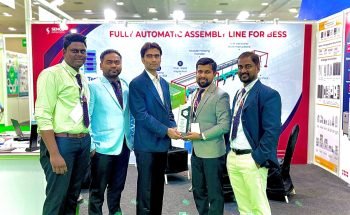
Renewable Energy Expo 2025

Bharat Mobility 2025
We Have Innovative Solutions For Future
Global Pioneers
Energizing the future with precision energy solutions since 2006.
Innovation Allies
Partnered with industry titans, Semco sparks brilliance in every circuit.
Tailored Excellence
Your energy needs met worldwide—Semco Infratech—Providing Precision and Perfection With Pride.
Contact Us
For any inquiries, questions, or recommendations, please call:
+91 11-4264-1452 or fill out the following form
Frequently Asked Questions (FAQs)
An automatic lithium battery assembly line is a fully automated production system designed to streamline the manufacturing process of lithium-ion batteries. It includes steps like cell stacking, laser welding, testing, and final assembly — ensuring high precision, safety, and scalability for industrial battery production.
A standard lithium battery assembly line includes:
- Cell loading and sorting
- Electrolyte filling
- Vacuum sealing
- Battery laser welding
- Formation and aging systems
This automation improves consistency and reduces labor costs in battery production.
A prismatic battery assembly line is tailored for producing prismatic lithium cells, commonly used in electric vehicles and energy storage systems. It handles processes such as cell stacking, pouch forming, ultrasonic welding, and precise casing of prismatic cells.
A BESS (Battery Energy Storage System) assembly line focuses on assembling large-scale battery modules and packs specifically for grid-scale energy storage. It involves modular pack integration, lithium battery laser welding, intelligent BMS installation, and rigorous quality testing.
An energy storage assembly line is designed to manufacture batteries for renewable energy applications like solar farms and wind energy systems. It supports high-volume production of battery modules with advanced automation and safety compliance.
Battery laser welding is a non-contact, high-precision welding method used to connect battery cells and terminals with minimal heat impact. It’s crucial for ensuring strong, reliable joints in lithium batteries, especially in automated environments like EV or BESS assembly lines.
Yes, lithium battery laser welding is suitable for cylindrical, pouch, and prismatic battery cells. It offers clean welds with high electrical conductivity and minimal material deformation, making it ideal for modern automated assembly systems.
Absolutely. SEMCO specializes in custom lithium battery assembly lines, including prismatic, BESS, and energy storage assembly setups. Our solutions are tailored to client-specific requirements, offering modular, scalable, and AI-integrated production systems.